At their most basic, valves are used to control the flow of liquids and gases, allowing for precise control of fluid flow rates and direction. They are essential components in many industries, including oil and gas, chemical processing, water treatment, and more. There are various types of valves available, each with its unique features and applications.
Common Valve Types
1. Gate Valve: Typically used when a quick shut-off is needed. The Gate Valve controls flow by lifting or lowering an internal gate. The gate is positioned perpendicular to the flow of fluid, blocking the flow when lowered and allowing the fluid to pass when lifted. This valve is typically composed of a valve body, bonnet, gate, and sealing components and is made from cast iron, cast steel or stainless steel for excellent corrosion resistance and wear resistance.
2. Globe Valve: Used to regulate the flow rate of liquids or gases and is typically used in situations where precise control of fluid flow is needed. The Globe Valve is composed of a valve body, bonnet, stem, and seat and controls flow by rotating the stem to adjust the size of the opening. The seat and disc form a tight seal when closed, and the flow rate can be adjusted by controlling the position of the disc. Globe Valves are typically made from cast iron, cast steel, or stainless steel for good mechanical properties and corrosion resistance.
3. Butterfly Valve: Used for controlling high-volume flow and is capable of quick opening or closing, and flow control through adjustment of the valve disc position. The Butterfly Valve typically consists of a valve body, disc, stem, and sealing components and is made from cast iron or cast steel for good flow and casting properties and has excellent durability and stability in high-pressure and high-temperature environments. The valve disc is positioned perpendicular to the flow of fluid, and the flow rate can be adjusted by rotating the disc. The disc is connected to a stem that rotates to control the position of the disc.
4. Ball Valve: Typically used when a quick shut-off is needed and consists of a ball, stem, bonnet, and sealing components. The Ball Valve controls flow by rotating the stem to open or close the valve, providing precise flow control. Ball Valves are typically made from cast iron, cast steel, or stainless steel for excellent wear resistance and corrosion resistance.
5. Check Valve: Used to prevent backflow. It typically consists of a valve body, a disc, and a spring. When the fluid or gas flows in the correct direction, the pressure pushes the disc away from the valve body, allowing the fluid or gas to pass through. When the fluid or gas flows in the opposite direction, the pressure pushes the disc against the valve body, preventing the fluid or gas from passing through. Check valves are commonly used in applications where it is critical to prevent backflow, such as in water or wastewater systems or in chemical processing plants.
6.Safety Valve: Used to prevent piping or containers from rupturing due to excessive pressure. It is designed to quickly open and release excess fluid when the pressure reaches a specific level, ensuring the system operates normally. This valve typically consists of a valve body, bonnet, disc, and spring, and is made from cast iron, cast steel, or stainless steel for high-pressure and high-temperature environments. The spring is adjusted to a specific tension to keep the valve closed under normal operating conditions. When the pressure in the system exceeds the set point, the disc is forced open by the pressure, allowing the excess fluid to escape.
7. Plug Valve: It is a quarter-turn valve used to control the flow of liquids or gases. It typically consists of a valve body, a tapered or cylindrical plug, and a stem. The plug rotates within the valve body to control the flow of fluid or gas through the valve. Plug valves are commonly used in applications where a tight shut-off is required.
8. Pinch Valve: Often used for handling solid materials, slurries, and liquids with suspended solids. They use a linear motion and typically feature an internal sleeve that isolates the media being transported, preventing it from coming into contact with the valve body. When the valve is open, the sleeve is compressed, allowing the fluid or gas to flow through the valve. When the valve is closed, the sleeve expands, completely blocking the flow of fluid or gas. This design makes pinch valves an ideal choice for applications where the fluid being transported is abrasive, corrosive, or contains suspended solids that could damage other types of valves. Pinch valve is not suitable for vacuum operation.
9. Needle Valve: Used to control the flow of fluids or gases in small-diameter piping systems. It typically consists of a valve body, a stem, and a needle-shaped disc. The stem is rotated to control the position of the needle-shaped disc, which can be used to precisely control the flow of fluid or gas. Needle valves are commonly used in applications where a high level of precision is required, such as in laboratory experiments.
Here is a comparison table that allows for a quick check on their respective applications:
Valve Type | Applications |
---|---|
Gate Valve | Used for quick shut-off and flow control in water, gas, and oil pipelines, power plants, and chemical processing plants. |
Globe Valve | Used for regulating fluid flow in HVAC systems, oil and gas pipelines, and chemical processing plants. |
Butterfly Valve | Used for high-volume flow control in water, wastewater, and chemical processing plants. |
Ball Valve | Used for quick shut-off and precise flow control in oil and gas pipelines, chemical processing plants, and water treatment facilities. |
Safety Valve | Used to prevent overpressure in pipelines and containers in oil and gas, chemical processing, and power generation industries. |
Check Valve | Used to prevent backflow in water and wastewater systems, chemical processing plants, and HVAC systems. |
Pinch Valve | Used for handling abrasive, corrosive, or viscous fluids or slurries in chemical processing, mining, and wastewater treatment industries. |
Needle Valve | Used for precise flow control in laboratory experiments, gas and liquid chromatography, and hydraulic and pneumatic systems. |
Plug Valve | Used for tight shut-off in water and wastewater systems, oil and gas pipelines, and chemical processing plants. |
How to Make A Valve: Valve Casting Process
Common manufacturing processes for valves include casting, forging, and machining. But casting is generally considered to be the most economical and commonly used manufacturing process for valve bodies. This is because casting allows for the production of large quantities of valves quickly and efficiently, and it is ideal for creating valves with complex shapes. Additionally, casting allows for the use of a wide range of materials, including cast iron, cast steel, and stainless steel, which makes it a versatile option for valve manufacturing.
However, casting itself has several different methods that can be used for valve manufacturing. These methods include investment casting, sand casting, and die casting:
Investment Casting
Investment casting, also known as lost-wax casting, is a casting method that involves creating a wax pattern of the valve body, which is then coated with a ceramic shell. The shell is heated to remove the wax, leaving a cavity in the shape of the valve body. Molten metal is then poured into the cavity, and once it has solidified, the ceramic shell is broken apart, and the valve body is removed and finished.
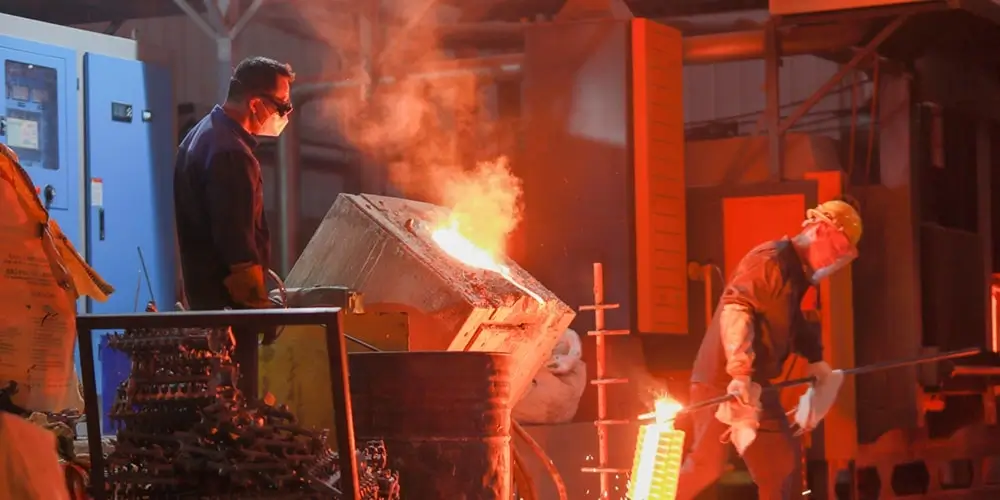
Here are the general steps involved in the investment casting process for valve manufacturing:
- Wax Pattern Creation: The first step is to create a wax pattern of the valve body using injection molding or other methods.
- Assembly: Once the wax pattern is complete, it is assembled with other wax components to create a tree-like structure, called a sprue or gating system, that will later be used to feed molten metal into the mold.
- Coating: The wax pattern and gating system are then coated with a ceramic slurry, which dries and hardens to create a shell around the wax pattern.
- Dewaxing: The ceramic shell is heated to a high temperature to melt and remove the wax pattern, leaving a cavity in the shape of the valve body.
- Preheating: The ceramic shell is then preheated to a high temperature to prepare it for the molten metal.
- Pouring: Molten metal is poured into the cavity in the ceramic shell through the gating system.
- Cooling: Once the metal has been poured into the mold, it is allowed to cool and solidify.
- Breakout: The ceramic shell is broken apart to reveal the finished valve body.
- Finishing: The valve body is finished by removing any excess metal and performing any necessary machining or finishing operations.
Each of these steps is critical to the investment casting process, and each step must be carefully controlled and monitored to ensure that the final valve body meets the necessary specifications.
Investment casting has several advantages as a method for valve manufacturing. For one, it allows for the creation of highly precise and complex valve shapes, making it a popular choice for creating customized valve designs. Additionally, investment casting can be used with a wide range of materials, including metals such as stainless steel, carbon steel, and aluminum alloys. However, investment casting can be more expensive and time-consuming than other casting methods, such as sand casting, and it requires specialized equipment and skilled labor.
Sand Casting
Sand casting is a traditional casting method that involves creating a mold made of sand and other materials. The sand casting process begins with the creation of a pattern, which is a full-sized model of the valve body made of wood, metal, or other materials. The pattern is used to create the mold by pressing it into sand to create a negative impression. The sand is then packed around the pattern to create the mold, which is then removed, leaving a cavity in the shape of the valve body.
Molten metal is then poured into the mold through a gating system, which allows the metal to flow into the mold and fill the cavity. Once the metal has cooled and solidified, the mold is broken apart, and the valve body is removed and finished by removing any excess metal and performing any necessary machining or finishing operations.
Sand casting has several advantages as a method for valve manufacturing. For one, it allows for the production of large quantities of valves quickly and efficiently, making it a popular choice for high-volume production. However, sand casting can result in lower dimensional accuracy and surface finish compared to other casting methods, and it may not be suitable for creating highly complex valve designs.
Die Casting
Die casting is a casting method that involves injecting molten metal into a mold under high pressure. The die casting process begins with the creation of the die, which is typically made of steel and consists of two halves that are joined together to form the cavity. Molten metal, such as aluminum, zinc, or magnesium, is then injected into the die under high pressure, which fills the cavity and forms the valve body. Once the metal has cooled and solidified, the two halves of the die are separated, and the valve body is removed.
Die casting has several advantages as a method for valve manufacturing. For one, it allows for the creation of highly precise and complex valve shapes, making it ideal for creating customized valve designs. Additionally, die casting is a high-speed process that can produce large quantities of valves quickly and efficiently.
Compared to investment casting and sand casting, die casting is typically used for smaller valve components due to its high precision and ability to create intricate shapes. While it can be more expensive than sand casting, it allows for the production of high volumes of parts quickly and efficiently, making it a popular choice for valve manufacturers. However, die casting requires specialized equipment and skilled labor, and it may not be suitable for larger valve bodies or more complex designs.
Other Manufacturing Process
Forging is like shaping metal with a giant hammer or press, which is great for making strong and durable valve components. On the other hand, machining is like giving a piece of metal a stylish haircut with cutting tools, which is perfect for creating precise shapes and finishes.
Forging
Forging involves heating and shaping metal using compressive force. This process is commonly used for Needle Valves, Safety Valves, and Check Valves. Forging creates strong and durable valves that can withstand high-pressure and high-temperature environments, so it is also recommended for creating valve stems, discs, and other components that require high strength and durability.
There are two main types of forging: hot forging and cold forging.
- Hot forging involves heating the metal to a high temperature, usually above its recrystallization temperature, which makes it more malleable and easier to shape. The metal is then placed between two dies, which are pressed together to shape the metal into the desired valve shape.
- Cold forging, on the other hand, does not involve heating the metal and is typically used for creating smaller valve components.
Apart from the strong and durable traits, forging also allows for greater control over the grain structure of the metal, which can improve the overall quality of the valve. However, forging can be a more expensive and time-consuming process than casting or machining, and it is typically only used for creating certain valve components rather than entire valve bodies.
Machining
Machining involves removing material from a metal block to create the desired shape. Machining is typically performed using computer-controlled cutting tools, such as lathes, drills, and mills. Machining is a popular choice for creating valve components such as stems, discs, and seats due to its ability to produce precise and complex valve shapes. It is particularly well-suited for Pinch Valves and other valves with a simple design.
The process of machining begins with a block of metal, usually a bar or a casting, which is mounted onto a machine tool. The machine tool is then programmed to move the cutting tool along the surface of the metal block, removing material to create the desired shape. The cutting tool may be a drill bit, a milling cutter, or a lathe tool, depending on the specific valve component being created.
Machining can be used with a wide range of materials, including metals, plastics, and composites. However, it is typically only used for creating certain valve components rather than entire valve bodies.
It’s worth noting that some valves may be manufactured using a combination of these processes. For example, a valve body may be cast, while the valve stem and disc may be forged or machined.
Valve Type | Casting | Forging | Machining |
---|---|---|---|
Gate Valve | ✔️ | ||
Globe Valve | ✔️ | ||
Butterfly Valve | ✔️ | ||
Ball Valve | ✔️ | ||
Safety Valve | ✔️ | ||
Check Valve | ✔️ | ✔️ | |
Pinch Valve | ✔️ | ||
Needle Valve | ✔️ | ✔️ | |
Plug Valve | ✔️ |
Note: This table is based on general trends in the valve manufacturing industry, and the cost and appropriate manufacturing process for a particular valve will depend on factors such as the valve design, material, and intended application
Valve Casting Material Selection
When it comes to selecting materials for investment casting of valves, there are a variety of options available depending on the application requirements. Generally, investment casting allows for the use of a wide range of materials, including stainless steel, carbon steel, and aluminum alloys.
For valves that will be used in corrosive environments, materials such as duplex stainless steel or super duplex stainless steel are commonly used due to their excellent corrosion resistance. In applications where high temperatures are expected, materials such as nickel-based alloys or titanium may be selected for their ability to withstand extreme temperatures.
Here are some characteristics of commonly used materials for valve bodies in investment casting, along with the types of valve bodies they are suitable for:
- Stainless steel: Stainless steel is a common material used for valve bodies due to its excellent corrosion resistance and durability. It is suitable for a wide range of valve types, including ball valves, gate valves, globe valves, and check valves.
- Carbon steel: Carbon steel is another popular material for valve bodies due to its high strength and good impact resistance. It is commonly used for gate valves, globe valves, and check valves.
- Duplex stainless steel: Duplex stainless steel is a corrosion-resistant material that is ideal for valve bodies that will be used in harsh environments. It is commonly used for gate valves, ball valves, and check valves.
- Super duplex stainless steel: Super duplex stainless steel is an even more corrosion-resistant material that is suitable for use in highly corrosive environments, such as offshore oil and gas applications. It is commonly used for gate valves, ball valves, and check valves.
- Nickel-based alloys: Nickel-based alloys, such as Inconel and Monel, are often used for valve bodies that will be exposed to high temperatures or corrosive environments. They are commonly used for ball valves, globe valves, and check valves.
The appropriate material for a particular valve body will depend on a range of factors, including application requirements, operating conditions, and cost considerations. By carefully selecting the appropriate material for the valve body, manufacturers can ensure that the valve will perform effectively and reliably over its intended lifespan.
Here is a common material comparison table for easier understanding of their differences:
Material | Characteristics | Suitable Valve Types |
---|---|---|
Stainless steel | Excellent corrosion resistance and durability | Ball valves, gate valves, globe valves, check valves |
Carbon steel | High strength and good impact resistance | Gate valves, globe valves, check valves |
Duplex stainless steel | Corrosion-resistant and suitable for harsh environments | Gate valves, ball valves, check valves |
Super duplex stainless steel | Even more corrosion-resistant and suitable for highly corrosive environments | Gate valves, ball valves, check valves |
Nickel-based alloys | High temperature and corrosion resistance | Ball valves, globe valves, check valves |
Conclusion
Valves are an essential component of many industrial applications, ranging from water treatment to oil and gas production. As such, the manufacturing of valves is a crucial process that requires careful consideration of various factors, such as the design, materials, and intended application. Common manufacturing processes for valves include casting, forging, and machining, with casting generally considered the most economical and commonly used process for valve bodies. Casting methods, such as investment casting, sand casting, and die casting, offer unique advantages and disadvantages, allowing manufacturers to choose the most appropriate method for their specific application. When it comes to material selection for investment casting of valve bodies, a wide range of materials are available, each with their own unique characteristics and suitable valve types. Ultimately, the appropriate manufacturing process and material selection will depend on a range of factors, such as the application requirements, operating conditions, and cost considerations. By carefully considering these factors, manufacturers can create high-quality valves that perform effectively and reliably over their intended lifespan.
SIPX foundry is a leading manufacturer of high-quality valves that are designed to meet the demands of various industrial applications. With state-of-the-art facilities and advanced manufacturing processes, SIPX foundry is committed to producing valves that are reliable, durable, and cost-effective. Whether you need ball valves, gate valves, globe valves, or check valves, SIPX foundry has the expertise and capabilities to deliver high-quality valves that meet your needs. Contact us today to learn more about our products and services, and discover why SIPX foundry is the trusted choice for valve manufacturing.